Optimization of material removal rate and surface characterization of wire electric discharge machined Ti-6Al-4V alloy by response surface method
Document Type
Article
Publication Title
Manufacturing Review
Abstract
Wire electric discharge machining (WEDM) is one of the foremost methods which has been utilized for machining hard-to-cut materials like Titanium alloys. However, there is a need to optimize their important operating parameters to achieve maximum material removal rate (MRR). The present paper investigates the effect of control factors like current, pulse on time (Ton), pulse off time (Toff) on MRR of machining of Ti-6Al-4V alloy. The study showed that, increase in current from 2 A to 6 A results in a significant increase in MRR by 93.27% and increase in Ton from 20 μs to 35 μs improved the MRR by 7.98%, beyond which there was no improvement of MRR. The increase in Toff showed a counterproductive effect. Increase in Toff from 10 μs to 30 μs showed an almost linear decrease in MRR by 52.77%. Morphological study of the machined surface showed that cut surface consists of recast layer on which microcracks were present, and revealed the presence of globules, ridge-structured formations of recast layers and voids. In addition, a regression model was developed to predict the MRR with respect to the control factors, which showed a good prediction with an R2 value of 99.67%.
DOI
10.1051/mfreview/2022016
Publication Date
1-1-2022
Recommended Citation
Doreswamy, Deepak; Sai Shreyas, D.; Bhat, Subraya Krishna; and Rao, Rajath N., "Optimization of material removal rate and surface characterization of wire electric discharge machined Ti-6Al-4V alloy by response surface method" (2022). Open Access archive. 4922.
https://impressions.manipal.edu/open-access-archive/4922
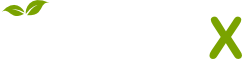
- Citations
- Citation Indexes: 17
- Usage
- Abstract Views: 1
- Captures
- Readers: 28
- Mentions
- News Mentions: 1