Optimization of the tool wear and surface roughness in the high-speed dry turning of Inconel 800
Document Type
Article
Publication Title
Cogent Engineering
Abstract
Machining of Inconel 800 superalloy is associated with inherent issues like lower tool life and lower quality of machined surface owing to the work-hardening nature of the superalloy and increased mechanical and thermal stresses. The employment of cutting fluid in machining negatively affects the locale. Hence, dry machining is a feasible alternate solution. This work aims to optimize the cutting parameters (CP): cutting speed, feed rate and depth of cut in the high-speed dry turning of Inconel 800 employing an uncoated carbide insert to minimize the responses: tool wear (TW) and surface roughness (SR). The superalloy machining is conducted as per the experimental runs designed applying the Taguchi analysis. Then, the effects and contributions of the CP on the outputs were examined employing the signal-to-noise (S/N) ratio and the analysis of variance (ANOVA). Additionally, the multi-objective optimization (MOO) method grey relational analysis was employed to optimize CP. The results of the research work showed that cutting speed, feed rate, and depth of cut have noteworthy sway on TW and SR with a % contribution of 33.3, 13.8 and 23.7, respectively. Additionally, evaluation of SEM images of the cutting insert revealed that the abrasion, adhesion and diffusion are the primary wear mechanisms leading to abrasion groves, crater, chipping, built-up-edge and notch formation.
DOI
10.1080/23311916.2024.2308993
Publication Date
1-1-2024
Recommended Citation
Prasad, Ganesha; Vijay, G. S.; Kamath, Raghavendra C.; and Hemmady, Harshit Jairaj, "Optimization of the tool wear and surface roughness in the high-speed dry turning of Inconel 800" (2024). Open Access archive. 7296.
https://impressions.manipal.edu/open-access-archive/7296
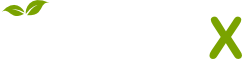
- Citations
- Citation Indexes: 8
- Usage
- Abstract Views: 1
- Captures
- Readers: 6
- Mentions
- News Mentions: 1