Optimization of Turning Parameters and Cooling Techniques for Enhanced Machining Performance of EN8 Steel Using L9 Orthogonal Array
Document Type
Article
Publication Title
Engineering Proceedings
Abstract
This study presents a detailed analysis of the effects of machining parameters, including the cutting speed (v), feed (f), depth of cut (d), and type of coolant flow (CF), on two primary performance characteristics in a machining process, namely, surface roughness (Ra) and material removal rate (MRR). A series of experiments were conducted, and the resulting data were analyzed using regression models, analysis of variance (ANOVA), Taguchi’s L9 orthogonal array analysis, and grey relational analysis. The initial findings from the raw experimental data revealed that, while Ra appeared to be influenced by a combination of parameters, an increasing trend in MRR was observed with higher values of feed rate and depth of cut. The regression models suggested the significant influence of the machining parameters on the Ra and MRR, with the type of coolant flow playing a critical baseline role. The ANOVA results statistically validated these models and ranked the significance of each parameter in affecting Ra and MRR. Furthermore, Taguchi’s analysis supported the findings and highlighted the potential for process optimization. The grey relational analysis revealed that the combination with a speed of 130 m/min, a feed of 0.1 mm/rev, a depth of cut of 0.15 mm, and a minimum quantity lubrication type of coolant flow provided the optimal result, with a GRG of 0.704, ranking first among all other parameter combinations, providing valuable insights for improving machining processes. The results, thus, indicated that the best results were generally obtained with higher speeds, lower feed rates, and moderate depths of cut under minimal quantity lubrication conditions. These findings could greatly benefit industry professionals in optimizing their processes for efficiency and quality, though it is noted that results may vary with different materials and machining conditions, presenting potential areas for future research.
DOI
10.3390/engproc2023059243
Publication Date
1-1-2023
Recommended Citation
Somayaji, Barkur Shrinivasa; Bhat, Ritesh; Naik, Nithesh; and Rajendra, Beedu, "Optimization of Turning Parameters and Cooling Techniques for Enhanced Machining Performance of EN8 Steel Using L9 Orthogonal Array" (2023). Open Access archive. 8629.
https://impressions.manipal.edu/open-access-archive/8629
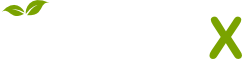
- Citations
- Citation Indexes: 1
- Usage
- Abstract Views: 3
- Captures
- Readers: 4
- Mentions
- News Mentions: 1